The shipping and storing of equipment, vehicles, and other assets often leaves them vulnerable to various types of damage. Whether protecting them from road debris and environmental factors during transit, or seasonal weather hazards during storage, ensuring the quality of your products with a protective covering that won’t fail is a crucial step in delivering the standard of quality your customers expect. Luckily, we’ve got the expert insight to help you prevent product damage that can lead to replacement costs, lost time and revenue, and unwanted inconvenience for you and your end customer.
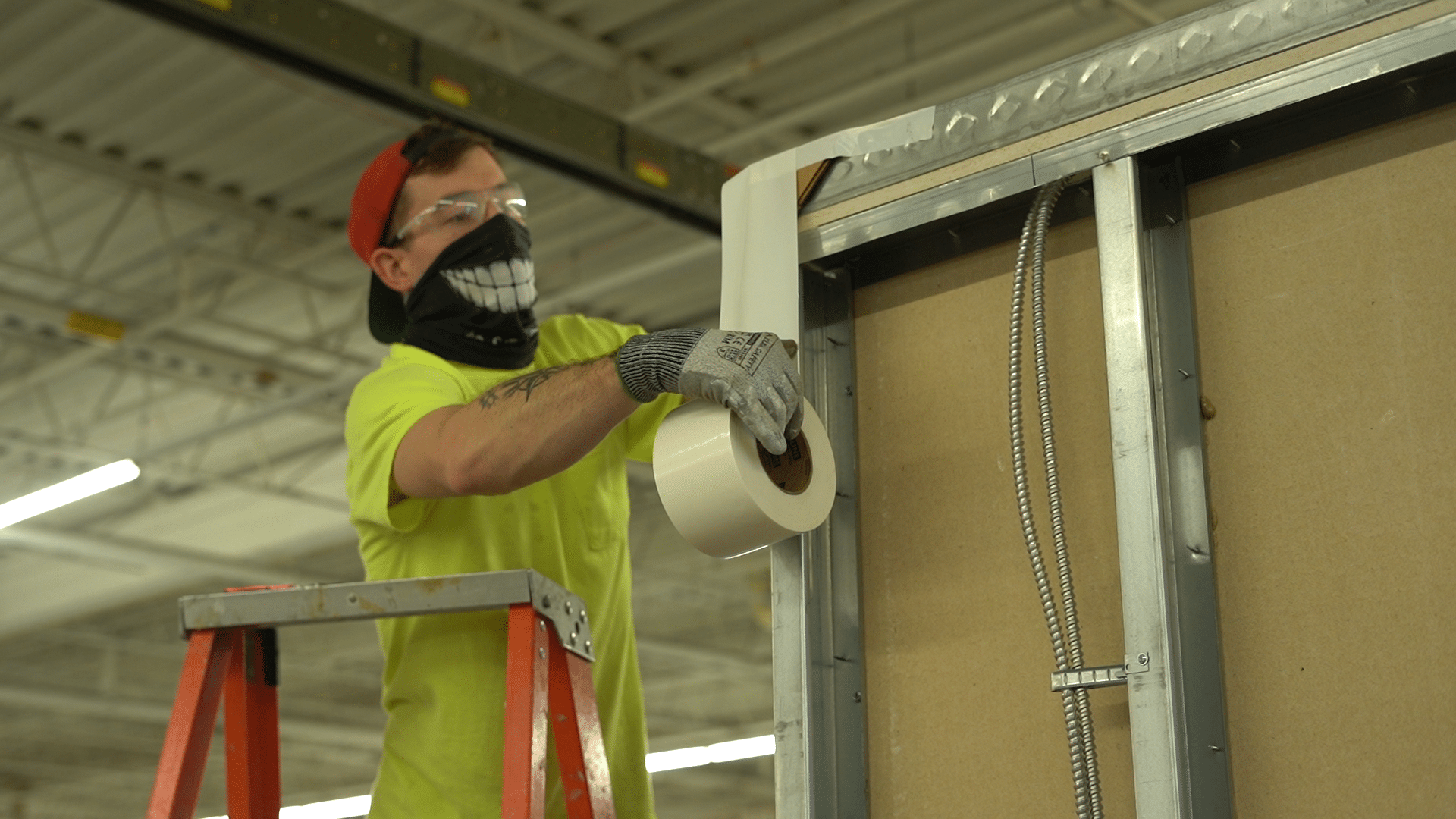
Leading causes of cover failures during transit and storage
Design
The first characteristic you should consider when choosing a protective cover for your assets is the design. One of the most common causes of cover failure is simply that the cover’s design is not effective for the item it’s meant to protect. When the design of the cover isn’t appropriate for the asset, the result is a poor fit, leaving the cover either too small, or loose and baggy. This only increases the chances of wind tunneling tearing the cover and leaving the asset exposed, or the cover blowing off completely during transit.
A poor design can also be ineffective for high-risk areas of an asset such as sharp edges, protruding elements, etc. The stress these areas put on an ill-fitting cover during high-speed transit and under high winds during storage, can lead to rips in the material and broken asset components – not to mention the additional damage surface exposure can cause.
Installation
Another leading cause of cover failure is improper installation. When it’s time to get an asset on the road, the installation of the protective covering can sometimes be rushed, leaving details overlooked and assets vulnerable to damage. One of the most common results of improper installation is an insecure fit which leaves air gaps around the perimeter of the cover. These air gaps increase the chance of wind tunneling and cover blow-off.
Hot and cold factors
When using heat-shrinkable covers and shrink wrap, burning can occur if overheated. This can lead to holes being burned right through the cover material which leaves your asset vulnerable to water leakage and buildup, wind tunneling ripping the material, and dirt and debris being blown against exposed surfaces.
During storage, the environment and weather in which the asset is being stored has a substantial impact if not properly protected. For example, outdoor storage during winter months presents its own set of hazards that only the right protective covering can withstand. Water buildup, snow, and ice add extra weight to protective covers and if they’re not up to the task, they begin to break under the pressure, leaving assets exposed to the elements.
Cover materials most likely to fail
Bottom-line interests sometimes lead manufacturers to opt for less-expensive covering materials like conventional shrink wrap or non-shrink material such as canvas. While these materials may help save money up front, their failure rate can lead to money lost down the road.
With shrink wrap, the pieced-together nature of installation and the thin nature of the material itself often makes it the most likely to fail during transportation and storage.
Non-shrink materials like canvas are normally heavier, making them harder to secure, causing more space for airflow and increased movement to occur during transit.
Avoiding cover failure to ensure quality
Being aware of possible damage scenarios due to ineffective cover choice is one thing – but what steps can you take to prevent them?
First, be sure to choose the best cover design for your asset. Consider the material your asset is made of, the method of shipping/storage, the environments it will be transported through and to, etc. Once you’ve determined the best cover design, pay close attention to the installation process. Protective covers can only perform at their best when they’re being used properly. Check for any holes that need to be repaired; ensure no air gaps are present; reinforce seams with tape; and pad or reinforce sharp or protruding areas of the asset.
For extra support and stability, you may want to create a structure around the asset to add an element of reinforcement outside the cover. You can do this by using a nylon strapping and pole system, or some other form of tenting method. Along with reinforcement, consider the position of the asset when it’s placed on a trailer or flatbed. Always choose the best positioning to utilize aerodynamics to your advantage. Cutting down on wind drag will help your cover resist movement and wind tunneling while traveling at high speeds.
Take damage out of the equation
The last thing any manufacturer wants is to cover, load, and ship an asset only to find out that it was damaged during transit and ultimately rejected by the end customer. That kind of price tag can be a big blow to your bottom line. Instead of risking that kind of loss, adopt a protective covering standard that takes all possibilities into account.
That’s exactly what our custom-fit covers have been designed for. Utilizing the most advanced cover technology in the industry, we’ve thought through every scenario you’ll come up against when shipping and storing your assets. From design and installation to environmental factors and risky weather, your assets will be able to ship and store while maintaining the same level of quality as when they left your hands.
Nathan is a Marine Sales Engineer with Transhield and focuses his energy on serving the marine industry throughout a large portion of the Midwest. His territory takes him everywhere from Minnesota to Arkansas. Prior to joining Transhield, he raced professionally on the OPC circuit.