Operators of CFM-56-3, -3B, and -3C variable stator vane (VSV) bores have until August 2018 to start an inspection process to help detect corrosion. This mandate was recently issued by the Federal Aviation Administration (FAA); now the aviation industry is even more attentive than usual to this enemy of aircraft. As MRO-Network reports:
“Corrosion has been found on the inside of the high-pressure compressor (HPC) case around the VSV bores resulting in binding, sticking, and seizure of the VSVs during engine operation,” CFM Int’l explains in the service bulletin, issued in April 2016 and updated in November, that FAA used to craft its directive. “The VSV system actuation check will aid operators in the early detection of excessive corrosion build-up on the inside of the compressor case and around the VSV bores.”
CFM International, a supplier of jet engines for commercial airplanes, strongly believes that such regular inspections are necessary only on aircraft that spend more than 50 percent of their time flying in tropical rainforest climate zones and operate less than 150 hours per month.
Even though in only one instance related to this corrosion has there ever been a reported problem, the FAA has nevertheless issued their directive mandating regular inspections. Moreover, this directive affects more than just this sub-group of engines, despite the request of CFM, Boeing, and Jet2.com, that the FAA limit the mandate.
Protecting expensive aircraft and their parts is a tough challenge. Sand, dust, rodents, moisture, corrosion, scratching, and etching are all hazardous elements due to outdoor storage. And constant flights in areas with high humidity increase the likelihood of corrosion. Therefore the FAA has recommended these regular checks, which requires rotating VSV actuation rings to ensure they move freely, at least every twelve months. If an inspection turns out some binding or sticking, checks will have to increase to each quarter, with repairs required within five flight cycles in the most extreme cases.
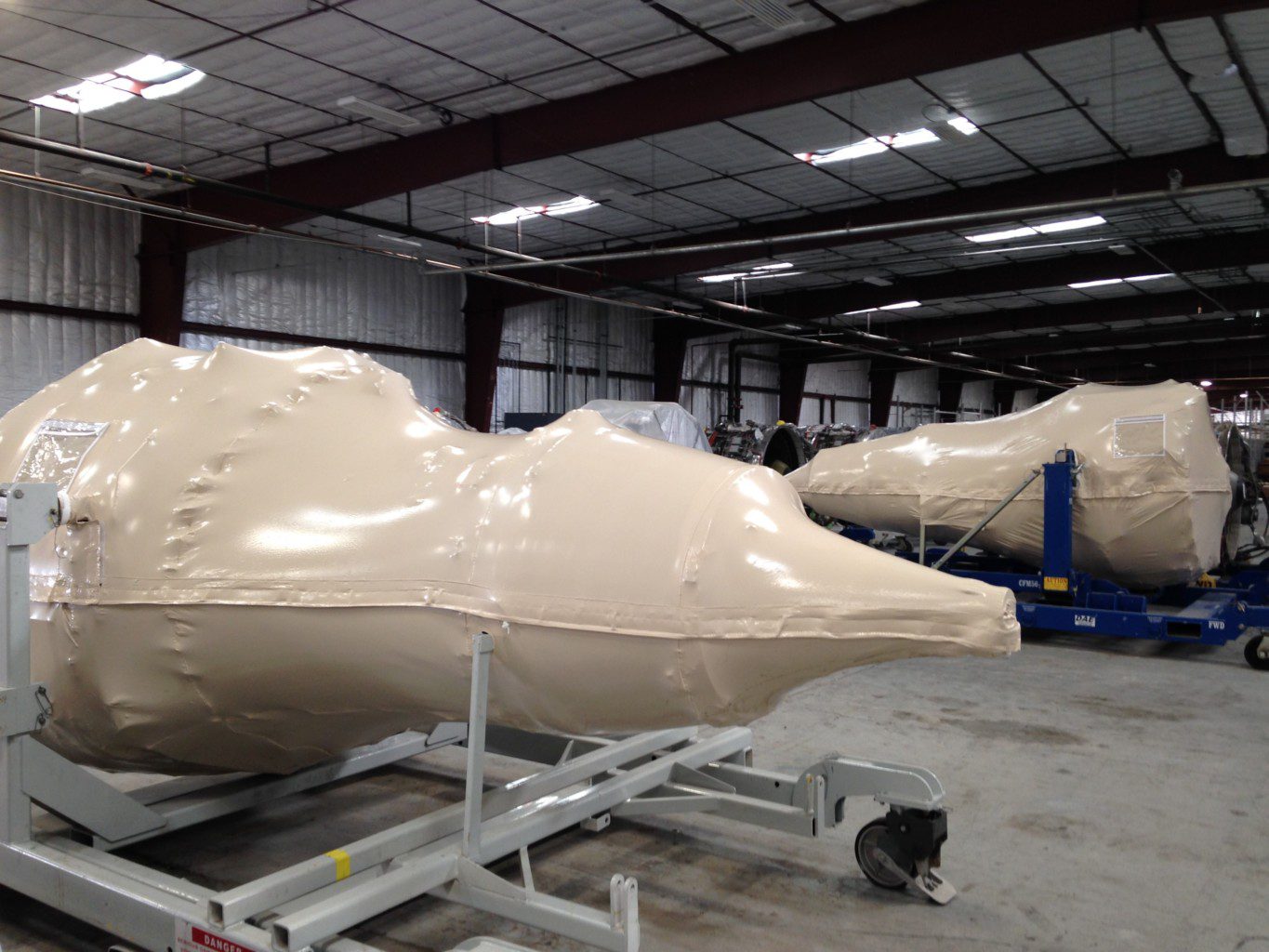
Ideally, aircraft operators address such issues before they cause safety concerns. Those who turn to Transhield covers will find the perfect solution and prevent these hazards from damaging a stored aircraft. Transhield covers keep aircraft equipment safe from environmental threats and allow serviceability during storage. The custom-fit covers are easy to install, and they provide a snug fit that keeps dirt and dust out of the equipment. And they are easily reinstalled once service is complete.
To learn more about how Transhield can help reduce corrosion in your aircraft, be sure to visit us online today!