The leading edge of architectural design and build are prefabricated pods. Born from the manufactured housing industry, modern pod evolution offers beautiful design, versatile use, and come in everything from stand-alone buildings to multiple pods that create homes, offices, and hospitals.
In an industry built on appearance and quality, other benefits to using pods in building are the speed, safety, and cost savings they offer a builder. Working in a centralized location allows for more supervision and quality control and worker proficiency. Common job site dangers are diminished on a controlled, well-supervised factory floor, plus this reduces the need for expensive on-site equipment. Finally, pod construction is completed inside, so work doesn’t stop because of weather conditions.
And with the speed that manufactured pod rooms can be built comes the need for speed and protection in pod shipping and pod storage. Let’s explore how builders protect prefabricated pods as they move from factory to build site and storage.
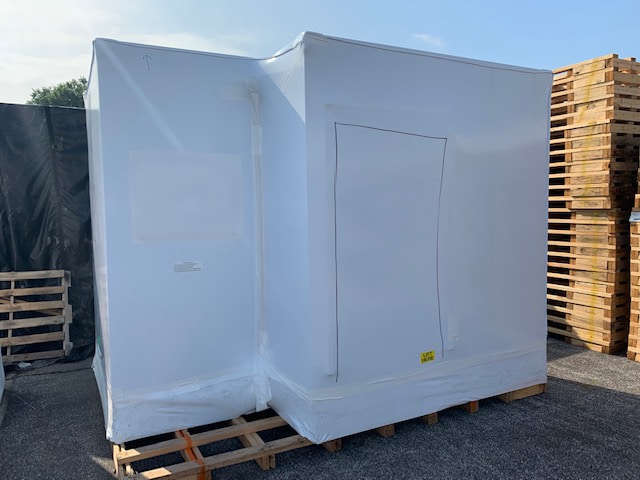
STARTING THE RIGHT WAY: PROPER APPLICATION
There’s no doubt that you’ve spent a lot of time building your prefabricated pods to the most modern design and build standards — you don’t want to cut costs at this point of the build process. As much as there’s a right way to build prefabricated pods, there’s a right way to protect your premium pod products.
Protective packaging is normally the last step in the manufacturing process before distribution — it’s important to get it right. Faulting on this step can mean costly warranty claims and a bad first impression from your customers. This requires careful planning to protect the modules as each prefabricated pod is completed in a climate-controlled manufacturing facility and will now be entering the elements. For the best protection, pods need to be individually wrapped in a waterproofing membrane to prevent moisture and debris from reaching them.
One benefit to Transhield fabric is that they offer strength and protection to large pod units; sometimes around 60’ long. And because they can be digitally designed utilizing 3D technology, manufacturers benefit from a perfect fitting protection solution that will create internal efficiencies, better consistency, and better quality in their packaging process.
This 3D modeling technology with Transhield fabric offers a water-resistant cover for all climates, condensation protection under the cover, a vapor corrosion inhibitor (VCI) additive to reduce corrosion, and protects from environmental damage including UV rays, dust, and rocks.
The shrinkable fabric is easy to use and quick to apply, saving staff time for other tasks.
THE ULTIMATE SHIPPING INSURANCE
A leading advantage of building prefabricated pods is that they are built in a quality-controlled factory environment with protection from the elements. But how is their premium quality safeguarded during transport? Once the pods are manufactured, they are wrapped in waterproof packaging and delivered to the job site where the building is being erected, completely weatherproof.
Using the 3D custom fit modeling technology — plus the shrinkable fabric — Transhield covers are perfect for providing aerodynamic transportation, especially for flatbed drivers that dislike the dangers of using tarps.
We know that traditional shrink wrapping and tarping often produce different results each time they are applied. Depending on the skill of the employee, the size and shape of the asset being covered, and shipping deadlines, the variance in consistency means there is more room for errors.
On the opposite end, once a cover is designed inside of 3D software, it can act as a template for future covers going forward. There’s no need to worry about a certain protection application fitting different than the other – they are all the same.
CUSTOMIZED STORAGE SOLUTIONS
The last step after delivery — and before a prefabricated pod is joined to its larger construction — is storage. Delivered modules are usually stored and staged on a neighboring lot, then unwrapped as required and craned and bolted to the building. This again leaves the prefabricated pod subject to the elements and risks lowering the quality of the module.
While some may argue shrink wrap can be less expensive, it’s also less efficient, less effective, and less durable. Transhield saves during this storage time because it protects from the elements and reduces costly warranty claims — making it far more economical in the long run.
As we mentioned before, the Transhield fabric offers water resistance, condensation protection, a VCI additive, and protects from environmental damage including harmful UV rays, dust, and rocks. This helps with the ultimate goal of keeping your prefabricated pod in the same condition as when it left the factory floor.
Transhield has years of experience in shipping and storage protection in the modular and prefabricated build space. We’re passionate about using technology to protect the unique products we ship around the corner and around the world.
SAVE BY SHIPPING WITH TRANSHIELD CUSTOM COVERS
Bottom line, if you’re shipping with standard vinyl and canvas tarps, you’re setting yourself up for more hassle down the road. By using Transhield custom protective covers with VCI technology, you’ll reduce the risk of surface damage and corrosion, and avoid higher long-term transportation costs. You’ll also increase the likelihood of shipping availability by not having to search endlessly for a vehicle and driver willing to haul a load that needs to be tarped. Your products and equipment can be shipped safely and show up with the quality your end customer expects.
Tyler has been with Transhield since 2006, currently serving the wind energy, HVAC, modular construction, power generation, and transportation markets; developing new business and supporting current clients in these verticals. Previous to his current role, Tyler served the aftermarket and marine industries at Transhield. Tyler is a graduate of the University of Wisconsin-Stevens Point.